6 Applications Where Auto Adjust Can Save You Tons of Time
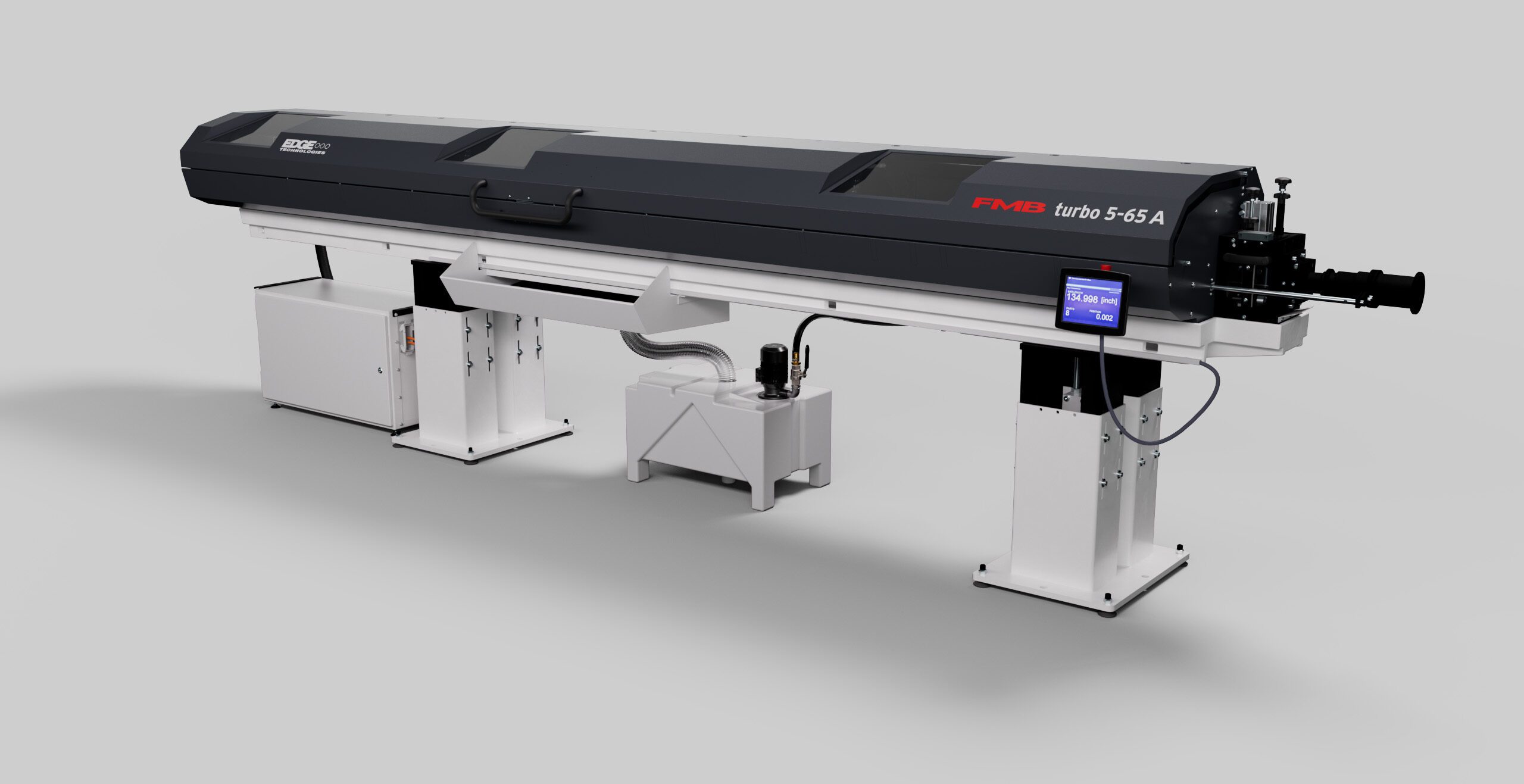
Guide channel changeovers can take time. Depending on the bar feeder model and condition, and the expertise of the machinist, they can take up to 30 minutes. And, many times, this isn’t a job for just anybody. It has to be scheduled with maintenance, which might spell half a day that your CNC lathe is down.
Plus, guide channel changeovers require quite a bit of organization: keeping them straight so they go back in same order and making sure all the sizes are correct (that you never overlapped your 38mm and 43mm). It can be done, but it takes patience and understanding.
That’s where the auto adjust feature comes in.
Auto Adjust technology can shrink that changeover time from 1 hour to five minutes. And the good news is, it’s been accepted for over 10 years, so it’s already proven its value. Let’s explore what it is and six applications where it might save you tons of time.
What Is Auto Adjust?
The Auto Adjust feature enables the channel to automatically change from one size to another. The guide channel defaults to the maximum allowable diameter. Using a controller, you change two parameters, a series of clam shells adjust through the bar feeder to your material size, and then you swap out the bar feed collet, and you’re on to your next job.
The Auto Adjust feature enables the channel to automatically change from one size to another. The guide channel defaults to the maximum allowable diameter. Using a controller, you change two parameters, swap out the bar feed collet, and you’re on to your next job.
6 Applications Where Auto Adjust Might Save You Tons of Time
1. If your production runs are small but many
We’ve seen many shops across all sorts of industries, from robotics to architecture to spaceflight, scrambling to meet customer needs around small, just-in-time quantities with tight deadlines – think lot sizes around 300 pieces. For a high-mix/low-volume shop to fulfill 400 of those orders in a day, an Auto Adjust can quickly earn its keep.
2. If you have hot jobs coming in a little hotter than they used to
Hot jobs are profitable and important when it comes to maintaining customer relationships. If you want to be the shop that’s easy to work with, known for being clutch on just-in-time manufacturing jobs, auto adjust can spell tailwinds for your shop.
3. If you have a shortage of employees to change out guide channel sets
Pre-pandemic, more people used to work shops, so machines could run with Band-aids. Since 2020, process has become the Holy Grail. The new standard is that a lathe can run without attendance. Auto Adjust meets that dynamic.
Auto Adjust allows you more flexibility. Rather than needing an extra operator to spend an hour changing the guide channel, or, worse, pulling away a programmer from programming, you can change it with two parameters.
4. If Engineering needs to switch on the fly from one job to another
Sometimes, one moment’s top priority becomes another. This is especially true for shops that produce parts made to order, where the next machine run is contingent on the latest order. Having the Auto Adjust costs you only five minutes, rather than an hour.
5. If you experience turnover on the shop floor
Changing over different size guide channels can be frustrating if you’re having to teach new employees the changeover techniques. Auto Adjust is intuitive, and smooths out the process.
6. If you want less waste
Changeovers are dirty, and many people on the floor don’t enjoy the task. We’ve witnessed shops that would machine down 0.90” of a 2” bar just so they wouldn’t have to perform a changeover. That’s terrible for the environment, tons of tool wear on your lathe and hardly worth it for how little you get back on scrap price.
Edge Technologies can guide you with Auto Adjust.
Auto Adjust works, and it’s lean manufacturing in a bottle.
The FMB Turbo 5-65 was one of the first bar feeders to come with the Auto Adjust feature. Ten years since it’s come out, the technology has only proven its value, and now the need is even greater, with hot jobs coming in a little hotter, employee shortages, and time more precious than ever.
Plus, in the case of the FMB Turbo 5-65, it is built on a cast-iron frame, making it one of the beefiest bar feeders ever created, with a steady rest on front and a frame that extends past the bar feeder so that the bars sit on a frame rather than sheet metal.
But don’t just take our word for it…
Hear Landon Martin, Machining Manager with United Brass Works, share how we helped him save 4 hours of production a day by moving to the Auto Adjust!
If you have any other questions, please do not hesitate to contact us. We are committed to giving you the tools and service you need so you can focus on high-quality products and exceptional service for your customers.