Bar Straightness and Other Things to Consider for High RPMs
To optimize CNC lathe RPM in bar fed applications, your bar stock should not have more than 0.007” total indicator runout per foot as measured at three equidistant points over the full bar length.
Here’s the inspection procedure for bar straightness:
- Place bar stock on three V-blocks spaced equidistance apart. For a 12′ bar, v-blocks would be placed 3′ (~1,000mm) from the ends and at the midpoint.
- Using a dial indicator, rotate the bar by hand 360 degrees measuring total runout at all three v-blocks.
- Runout should not exceed 0.028” at any v-block.
You can use this helpful diagram on your shop floor:
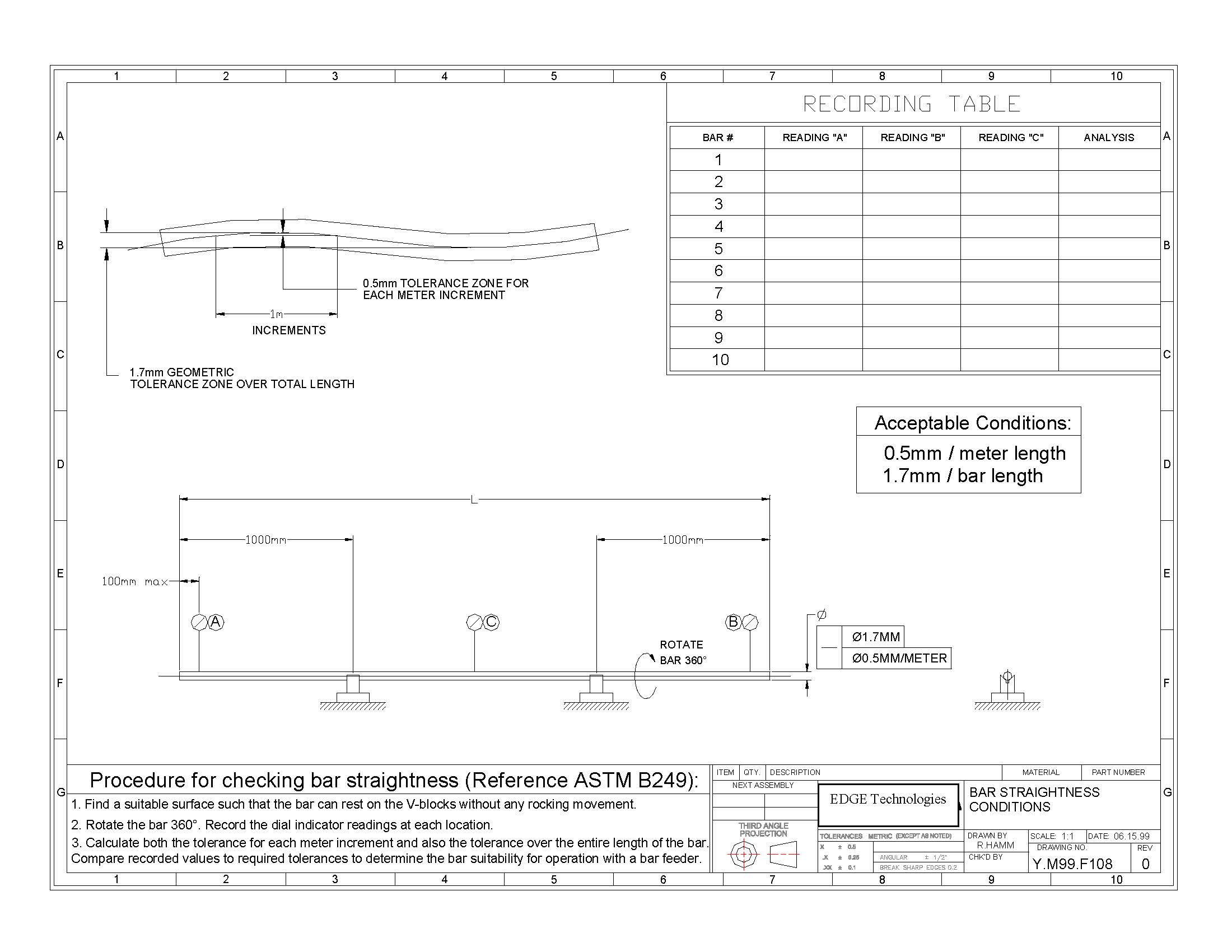
Bar straightness: To optimize CNC lathe RPM in bar fed applications, your bar stock should not have more than 0.007” total indicator runout per foot as measured at three equidistant points over the full bar length.
Other Considerations to Maximize CNC lathe RPM:
- Saw-cut ends are generally preferred over sheared bar ends, as sheared ends can create a kink or bend at one end of the bar length when the shear becomes dull. The end sections of the bar stock are more likely to cause vibration issues.
- Use the right sized guide channel set. This can effect RPM performance dramatically.
- Use the recommended oil viscosity for your bar feeder model. This makes a difference in stabilizing the rotating bar in the guide channel set and achieving the hydrodynamic effect.
- Use recommended oil pressure settings. Too much pressure with small-diameter bars can cause vibration. Too little pressure on bigger diameter bars diminishes vibration dampening.
- Set your roller steady rest correctly and / or use the correct sized bearing block and telescopic nose insert.
- Tweak the part program / sequencing to minimize harmonics.
- Ensure that chuck pressure is set correctly.
Use this checklist below for the best possible performance, or reach out to edgehelp@edgetechnologies.com to schedule a preventative maintenance review:
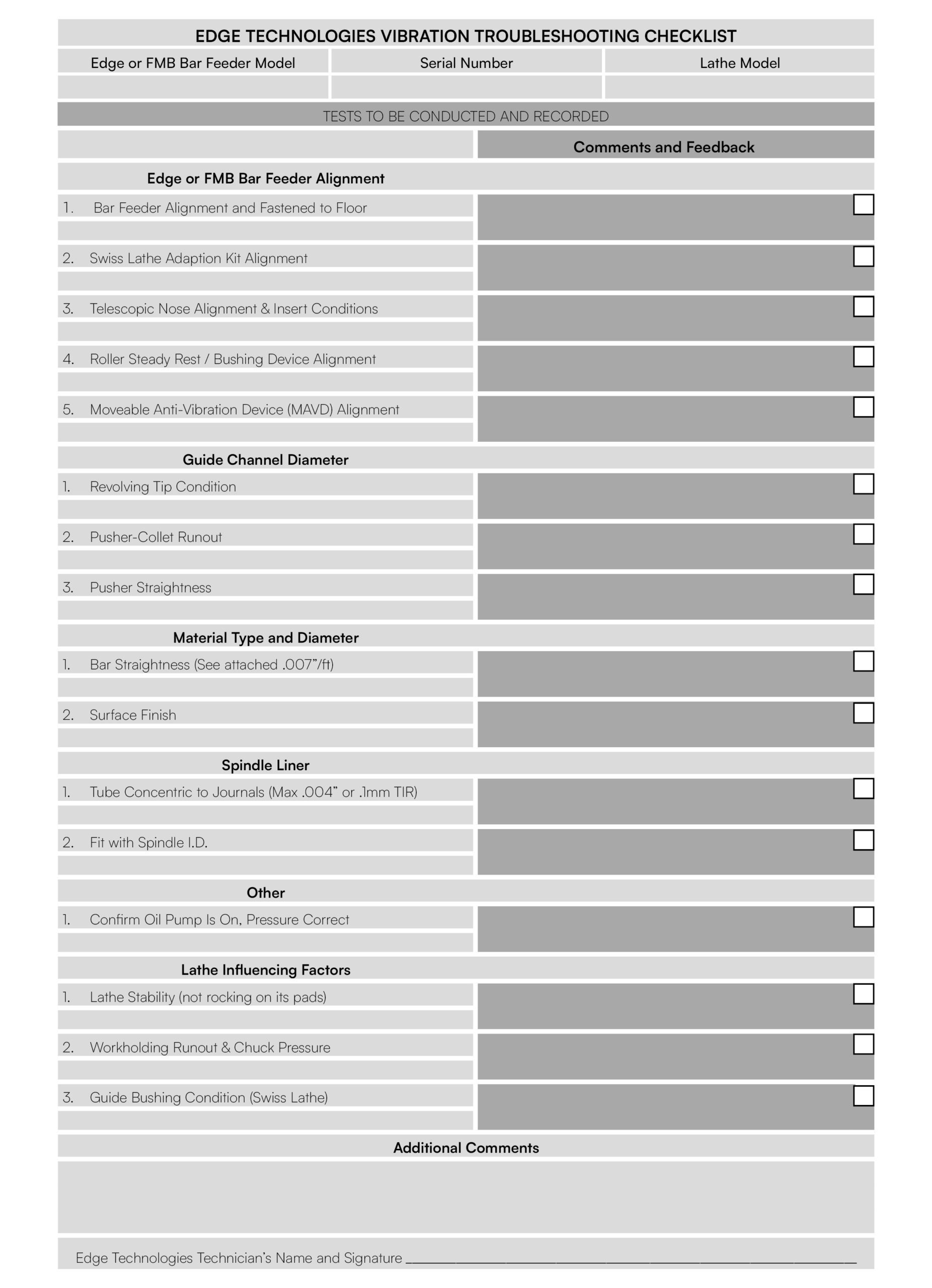