How Hydraulic Oil Achieves the Hydrodynamic Bearing Effect on CNC Lathes
In high-speed CNC lathe operations, 12 and 6 ft bar feeders use hydraulic oil to achieve the hydrodynamic effect (sometimes called the hydrostatic effect). The hydrodynamic bearing effect keeps the bar stock spinning smoothly. A thin layer of oil forms a pliable barrier between the bar and the guide channel, which reduces friction, cuts down on vibration, and cushions the bar as it rotates.
Bar feeder oil helps:
- Keep the bar centered.
- Reduce wear on both the bar and the bar feeder.
- Ensure smoother, more stable rotation, especially at high speeds.
We recommend hydraulic oil because it is accessible, affordable, and comes in different viscosities.
The diameter of the bar is important, and so is bar straightness (but that’s another topic). Larger bars fit more tightly in the guide channel, so they need just the right amount of oil to prevent friction. Smaller bars have more clearance, but too much oil can cause them to become unstable. Because of this, make sure you select the right guide channels for your setup.
First, consider your bar size range. With the Edge Technologies Scout 320, a common setup is a 14mm channel covering 1/8″ to 3/8″, and a 24mm channel covering 7/16″ to just over 3/4”. In this setup, the changeover point is 3/8″.
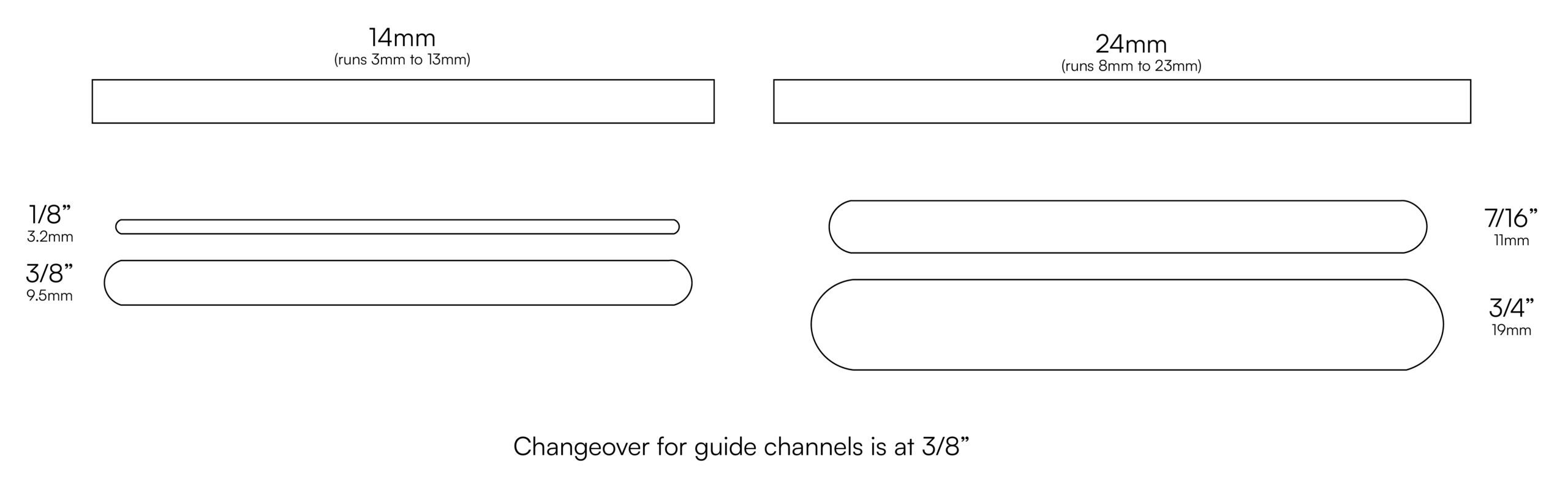
The hydrodynamic bearing effect: A thin layer of oil forms a pliable barrier between the bar and the guide channel, which reduces friction, cuts down on vibration, and cushions the bar as it rotates.
Why? Because the guide channel must be a bit bigger than the bar — if it’s too tight, the bar won’t spin freely, which can cause wear or even jamming. If it’s too loose, the bar can vibrate or “whip” (bend and flex as it spins), which hurts both accuracy and surface finish.
Next, choose the correct oil viscosity. Smaller bars require a lighter oil, generally ISO 68 cST, with bars smaller than 1/8” even requiring ISO 32 cST. Heavier bar stock requires ISO 150 cST. Generally, Edge Technologies bar feeders use between ISO 100 cST and ISO 150 cST.
Bar feeder oil enables you to achieve the hydrodynamic effect. Not only does the oil lubricate the bar, it also stabilizes it, helping you achieve smoother, more accurate production at the highest possible RPMs.