Customer Testimonial
Over 75,000 Hours of Unattended Production Time: Edge Technologies Helps Custom Tool Inc. Add 50% More Capacity Without a Full-Scale Capital Investment
Compay Name: Custom Tool Inc.
Website: https://www.customtoolinc.com/
Custom Tool Inc. is a trusted supplier of precision metalworking services and machined component parts based in Cookeville, Tenn. With their core competencies in CNC machining, turning, milling and Swiss turning, they manufacture for automotive fuel and filtration systems, oil field valves, surveillance equipment, and military hardware. Differentiators include precision machining requiring <0.001″ tolerances, account managers assigned to every customer, 95% on-time delivery, and rapid response when extreme circumstances demand it.
In 2010, Bob Young and his brother Gillen Young purchased Custom Tool Inc.
Bob set to work investigating the company’s current state and imagining ways they could streamline processes. That same year, at IMTS, they purchased their first piece of automation – Edge Technologies’ debut Patriot 338 bar feeder, an eight-footer on the display floor in an American flag wrap.
Bob chose Edge, because he appreciated that Edge offered a two-tier product line, with high-end bar feeders as well as entry-level options. He also appreciated the service and support he received throughout the journey.
Since then, anytime they’ve needed a new part or a diagnosis on an issue, Edge has been extremely responsive. Bob knows the service guys on a first-name basis, and the service guys stay on the phone until the issue is resolved.
“The parts department is just stellar,” Bob said. “I’ve never had to wait a long time. Generally, if something happens in the morning, we have a high degree of confidence that the part will arrive within 24 hours.”
Unattended Production on Multiple Material Sizes, Including Hex
Today, Custom Tool Inc. boasts 3 Patriot 551s and 1 Patriot 338 running on Okuma LB3000 EX II-MYWs, and an 8’ Patriot 338 running on an Okuma ESL6 II. Three of the bar feeders have the flag wrap. Custom Tool Inc. also has an FMB 5-65 on an Okuma Multus B250II.
The bar feeders have allowed Custom Tool Inc. to run unattended production on multiple material sizes, including hex, said Clay Adcock, Manufacturing Manager. On the Patriots, two guide channel sizes cover them from 3/8” to 1”, empowering them for long production times.
Not only do the bar feeders allow long production times, they have helped Clay run two-operation processes on the lathes.
Likewise, the FMB “is a beast of a bar feeder,” Clay said.
Clay loves that it has a brake function to keep it from pushing back into the chuck, especially when he’s performing drilling operations. The cast iron base offers extra rigidness, which helps reduce vibrations, making it great for bigger parts that have more geometrical features. The axial shift accessory allows him to change a spindle liner in 15 minutes rather than 1 hour.
“Without these bar feeders, we would not be able to run unattended,” Clay said.
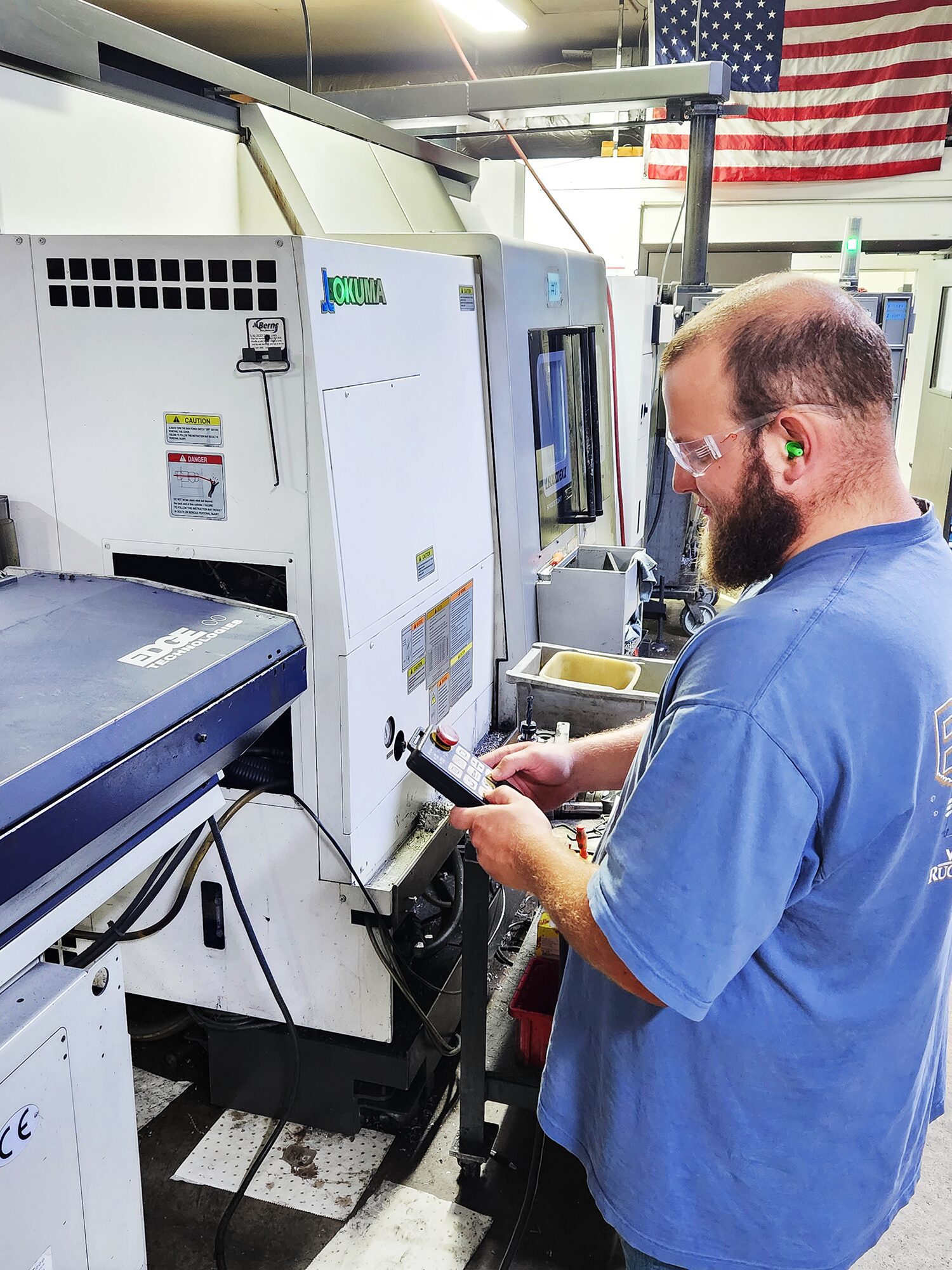
“We probably have over 75,000 hours over the past 10 years of unattended production time. We’re easily adding 50% more capacity than what we had otherwise. And it didn’t require us to go full scale capital investment to get that done.”
“Allowed Us to Put Humans in Areas Where the Machines Can’t Perform”
At the end of the day, the bar feeders have allowed Bob and Clay to maximize utilization when people aren’t in the building, Bob said.
“We have confidence that the bar feeders will perform when they are scheduled to, to load a bar, to drop or pull out remnants, to set correct measurements of the bars passing through the flag,” Bob said. “They are highly dependable.”
In other words, the bar feeders have allowed them to put humans in areas where the machines can’t perform.
“We probably have over 75,000 hours over the past 10 years of unattended production time,” Bob said. “We’re easily adding 50% more capacity than what we had otherwise. And it didn’t require us to go full scale capital investment to get that done.”