Customer Testimonial
Edge Technologies Helps Liberty Precision Manufacturing Run Full Speed to Lights Out Production and Beyond
Compay Name: Liberty Precision Manufacturing
Website: https://www.libertyprecision.com/
Liberty Precision Manufacturing is an aerospace subsidiary of Pindel Global Precision based in New Berlin, Wis., focused on some of the most demanding customer parts produced at volume – complex features, tolerances and materials at volumes between 1,000 and 100,000 pieces a year.
Liberty Precision Manufacturing focuses on challenging customer parts, so, if you ask CEO Bill Berrien what’s most important, he’ll say quality and quick turnaround at the best price.
To achieve that, Swiss Production Supervisor Darrin Baker envisioned all operations running under a uniform brand in the Swiss department, to make training and onboarding as easy as possible.
Today, Liberty Precision Manufacturing runs:
- 2 Minuteman 320s on BE20Vs
- 1 FMB Turbo 5-55 on a Tsugami B038T
- 1 FMB Turbo 5-55 on a Tsugami B0386
- 2 FMB Turbo 3-38s on Tsugami B038Ts
- 1 FMB Turbo 3-38 on a Tsugami SS327
- 1 FMB Turbo 3-38 on a Tsugami BW329Z
- 2 FMB Micromag 20s on Tsugami S206s
- 1 FMB Micromag 20 on a Tsugami B0126-V
- 1 FMB Micromag 20 on a Tsugami B0205-V
Of their 15 Swiss machines, 12 have Edge Technologies bar feeders. The other 3 are competitors.
Parameters that Are Easy to Work with
Prior to Liberty Precision Manufacturing, Darrin had only worked with a competitor bar feeder.
“I knew the evils, but I just figured they were something you had to accept,” he said.
When Darrin started at Liberty Precision Manufacturing, the shop had an array of bar feeder brands. Darrin explored the unique qualities of each.
Quickly, he discovered that the “evils” of the competitor bar feeder were not universal.
For example, one “evil” included parameters. Titles were unclear, and Darrin had to program negative numbers for facing values to work, which made no sense to him.
“It’s very hard to train people on those,” Darrin said.
But the FMB parameters were easy to work with. Very few parameters (maybe four) needed to be adjusted every time. And that kind of ease helped improve things like remnant control.
Choosing FMBs as part of the uniform brand for the Swiss department made sense.
FMB – Perfectly Engineered for High Utilization Rates
At his old shop, whenever Darrin tried to run bars at an optimal rate, the competitor bar feeder would rev up the bar.
“You’d try to hit 8,000 rpms, and it would get so loud, that bar whip would sound like it was going to destroy everything,” Darrin said.
In contrast, the Liberty Precision shop is surprisingly quiet.
“This allows us to run full speed with no worry, which means more parts, more dollars a day – and not just more parts but higher quality, less chatter, longer tool life,” Darrin said. “Not having the bar feeder be the limiting factor, that’s critical.”
This has allowed for high utilization rates.
For example, Liberty Precision Manufacturing makes 400 different part numbers annually for one Fortune 100 customer, an aggregate piece count in the single-digit millions. Liberty Precision Manufacturing has had, year-to-date, 0 dpm (defects per million).
“That’s huge for that level of volume,” Bill said.
For the FMBs, it’s a combination of proper engineering and high-quality components.
“Proper engineering takes complex processes and makes them so simple a child can use them,” Darrin said. “And then the FMB uses quality components on top of that.”
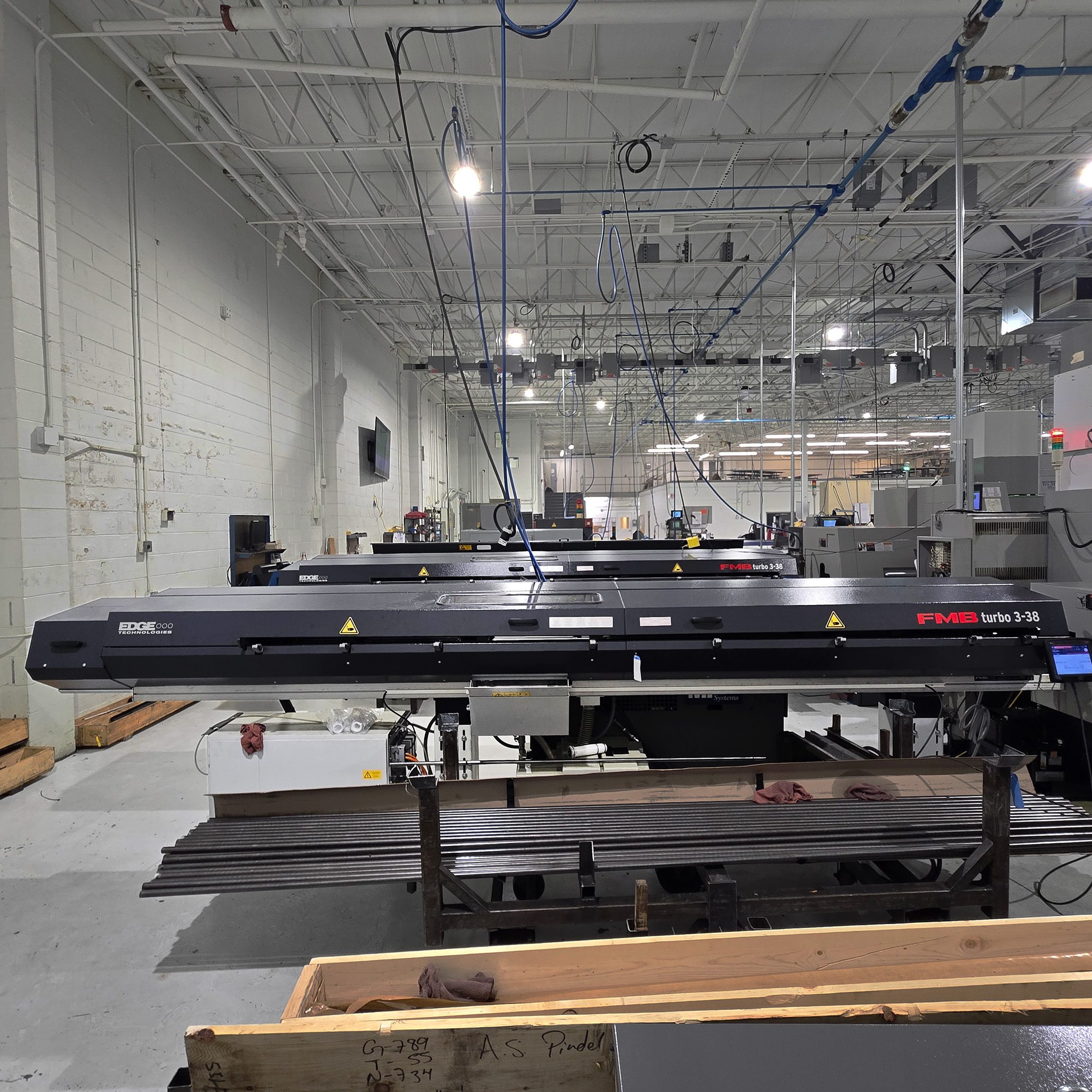
“The FMBs allow us to run full speed with no worry, which means more parts, more dollars a day – and not just more parts but higher quality, less chatter, longer tool life. Not having the bar feeder be the limiting factor, that’s critical.”
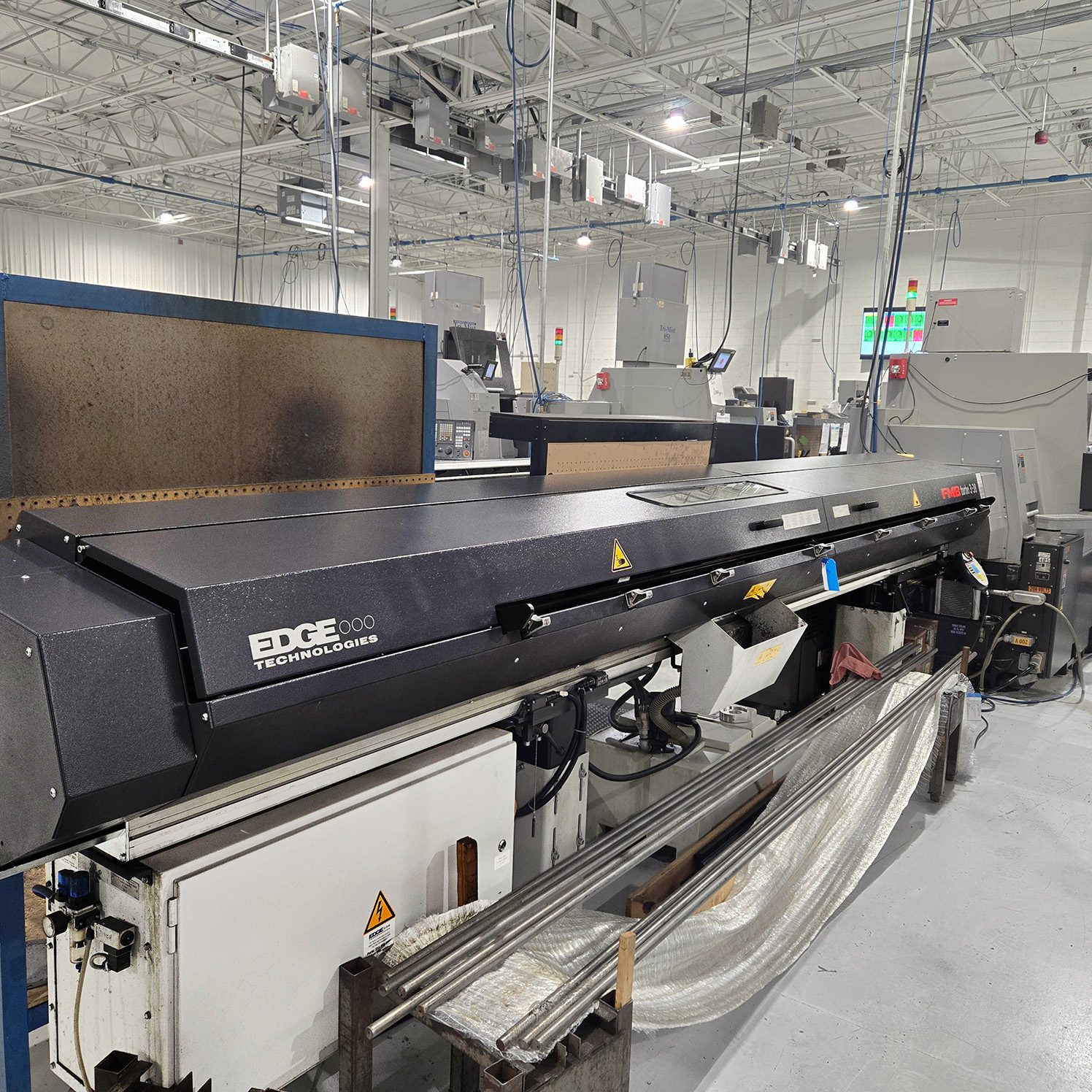

Edge Technologies Regional Service Approach Helps with Training
Since Covid-19, training has been integral to the success of the machine shop.
“You hire for attitude, train for skill,” Darrin said. “Edge Technologies has made that super simple.”
Edge Technologies has over 40 regional service technicians, the largest in the bar feed industry. Darrin has worked with a technician during installations and service calls, and gained valuable insight each time.
For example, when Liberty Precision Manufacturing adopted the FMB Micromag 20, a technician trained the team on using pilgrims (a walking beam separation device for feeding small-diameter bars). And when Liberty Precision Manufacturing added a steady rest on the lathe side to further reduce vibrations, the technician aided in the necessary parameter adjustments.
He’s even responded off-hours to emails.
“That’s above and beyond service,” Darrin said. “He’s helped us to become a better team, to get stuff up and running and to make sure we understand the new technology.”
Lights Out Production
Four days a week, Liberty Precision Manufacturing runs 20 hours of manned production across two shifts, followed by lights out production for the remaining four. They’ve also implemented an incentive program for employees to monitor unattended production during the weekend.
Under Darrin’s leadership, throughput increased by 200 percent. Since then, Liberty Precision Manufacturing has posted record numbers every single year.
“You don’t get that if you’re still experimenting with bar feeder types,” Darrin said. “You find a good product, and you stick with it.”
Industry 4.0 and Beyond
Bill believes that high levels of automation, highly utilized, and made so by a highly trained, highly paid team will enable Liberty Precision Manufacturing and other Wisconsin manufacturers to produce product at or below the price of lower-wage countries, leading to Wisconsin being a manufacturing powerhouse to the world (again). Automation has already liberated employees from manual repetitive processes to focus on areas that drive more value, he said.
“We stumbled across a mistaken belief in society that what you learn in the first 25 years of life will last you the next 50,” Bill said. “That might’ve been the case when life expectancy was 40. But personal interests change, technology changes – how do we support the lifelong skills of those already in the workforce? FMB bar feeders are integral to this, as they are easy to train new talent and support profit growth (via lights out production and other productivity-enhancing strategies) that allow us to invest deeply in continuously upskilling our talent.”
In the last eight years, the team has seen a renaissance in manufacturing, a renewed appreciation for work being done in the United States, Bill said. And Edge Technologies has contributed to that.